This article was originally published on StateCollege.com on April 22, 2020. You can read the original at the following link: http://www.statecollege.com/news/local-news/local-initiative-continues-to-help-with-production-of-ppe-for-covid19-response,1483081/
Like anyone living in a time of need, Tim Simpson, Paul Morrow Professor of Engineering Design and Manufacturing in the College of Engineering, asked himself the question “how can I help?”
The answer: turn his 3D printing course into a small part of the supply chain for personal protective equipment like face shields and masks needed to protect health care workers and others from COVID-19.
As a result an initiative — called Manufacturing and Sterilization for COVID-19 (MASC) — began as he instructed his undergraduate 3D printing course to help with the cause.
“It was going to be tough to run a hands-on lab when students weren’t allowed in the labs, so I started looking for ideas about 3D printing COVID-19 PPEs, which students can help design from their homes,” he said. “My students jumped at the opportunity to focus their project on this pressing need.”
Like all things related to Penn State, once the ball got rolling it picked up steam. Suddenly others were on board and a network of printers and minds both inside State College and beyond took up the cause.
Take for example The Rivet at Discovery Space in State College which is serving as a drop-off point for community made PPE items. In addition, a partnership between The Rivet and Actuated Medical has allowed for the production of hundreds of face shields.
“It has been great connecting with other local groups and regional efforts to address PPE and other supply chain shortages for COVID-19,” Simpson said. “That has expanded our group to over 350 people on our listserv, 315 users on our Microsoft Teams channels, and a network of over 150 3D printers that I can tap into at a moment’s notice.”
“We have made 300, maybe 400 face shields for the community that have been distributed and more requests still to fulfill,” Michele Crowl, executive director at Discovery Space said. “Our goal is to get them out to anybody who needs them, but especially nonprofits and local, smaller businesses that don’t have access to any national supply.”
Like all things, creating PPEs and face shields doesn’t happen without a cost. A MASC Fundraising Campaign has already launched to help fund the ongoing efforts once initial resources are used up. For example, finding the right kind of plastic for the face shields has been a challenge and will continue to be as efforts nationwide continue.
The good news: the success of the project has allowed Simpson to focus his class on other COVID-19 related tasks and solving different problems during the ongoing crisis.
“Ear savers (strap adjusters) for instance to improve the fit of a surgical mask,” Simpson said. “Or spool up a team to develop a replacement for a device or component that will soon be out of stock. In several cases, we have gone from need to idea to working prototype for feedback in 2-3 days. Everyone is amazing!”
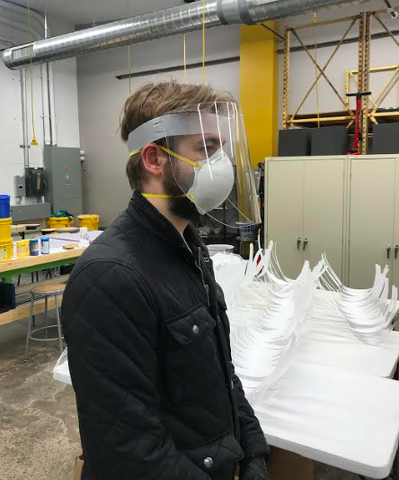